Health & Safety Consultancy Services
HSE
Health & safety consultancy services
Did you know that the law requires you to appoint at least one Competent Health and Safety Person in the workplace? Using external health & safety consultants costs companies less than getting fined for breaching their legal statutory duty.
Our health & safety consultancy services will provide you with up-to-date, relevant, hands-on, easy-to-apply advice.
They will guide you every step of the way on how to manage general or specific aspects, such as:
- Accident/incident investigation support – A3 process
- Business Continuity Plans (BCP)
- COSHH awareness training
- Emergency Response Plans (ERP)
- Fire Risk Assessments (FRA)
- Fire safety improvement plans
- Fire warden and fire marshal training
- Health and safety advice
- Health and safety compliance audits
- Health and safety documentation and policies
- Health and safety documentation preparation and support
- Health and safety improvement plans
- Health and safety training
- ISO 45001 Safety Management System Preparation
- ISO 14001 Environmental Management System Preparation
- ISO 9001 Quality Management System Preparation
- Responding to an act of terror
- Risk assessing
- Risk assessment training
- Safety Management System (SMS) Design
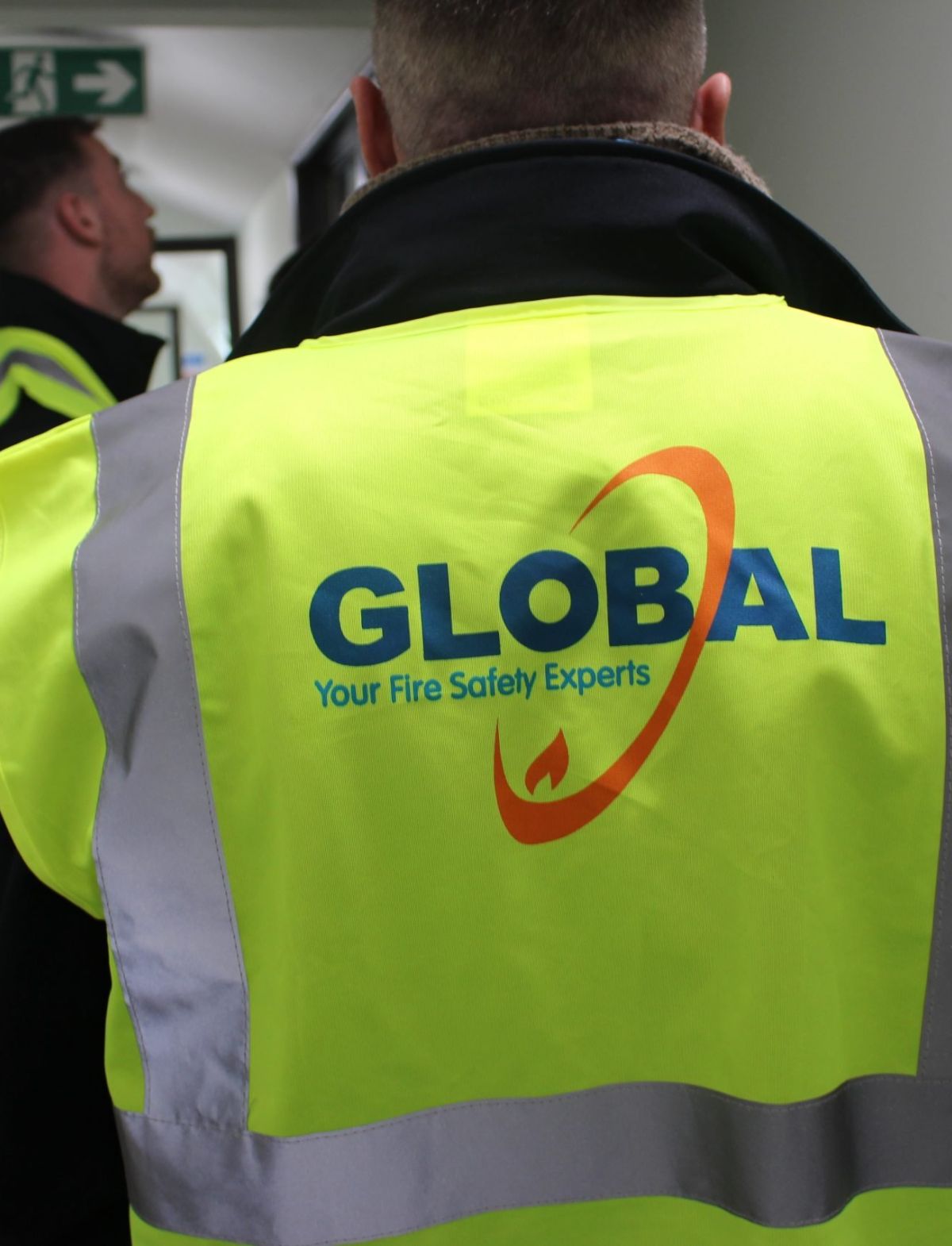
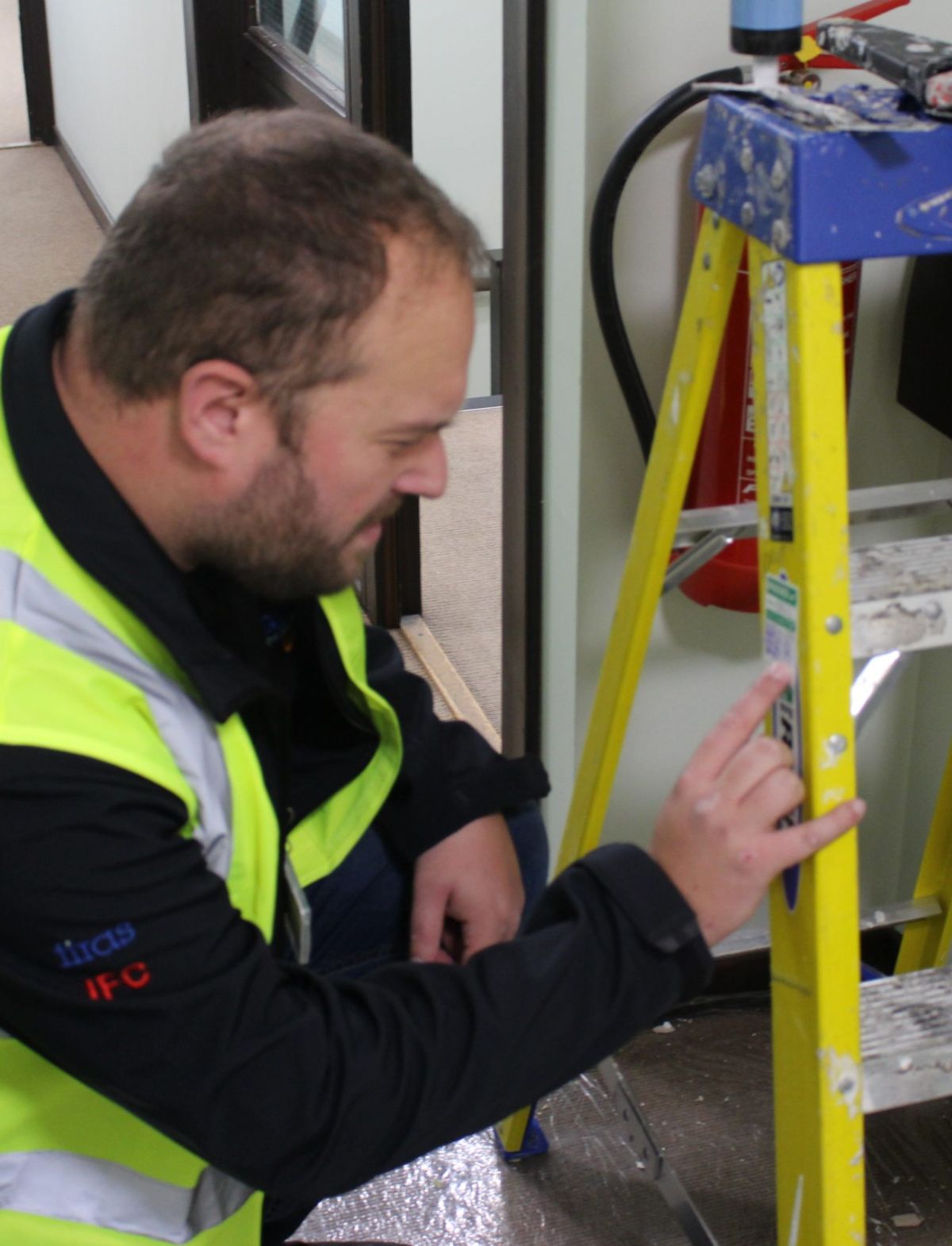
HSE
Tailored services that help you:
- Assess risks to your employees in the workplace.
We visit your business premises in person and carry out health and safety risk assessments to identify relevant risks to your staff and visitors. - Minimise risks and prevent harm.
Our consultants advise you on practical actions to protect your employees and prove compliance. - Write your health & safety policy.
We focus on practicality and implementation when creating your policies, as well as keeping your business in line with the law. - Access competent health & safety advice.
We guarantee clear, concise, 24/7 available advice. - Monitor and review your policies.
We make it easy to constantly update and streamline your health & safety systems while staying in line with the law.
Our consultants
- Hold Disclosure and Barring Service (DBS) Enhanced.
- NEBOSH & IOSH qualified.
- ISO Auditors
- IOSH members.
- BOSH P402 asbestos surveyors.
We Have PI Insurance to £10 million
HSE
Meet Chris
HSE Experience:
Chris started is HSE career in 2015 as a Non-Comissioned Officer in the Royal Air Force. Chris worked on sites across the UK conducting audits, inspections and safety projects across: accommodation, engineering facilities, city centre offices, aircraft hangars and specialist maintenance facilities. Chris Joined Amazon UK in 2021 as a Multi-site Workplace Health and Safety Manager, managing HSE requirements at distribution centres across the midlands. Chris was involved in international risk assessment projects and setting up safety management systems for new sites. Chris joined Global HSE Solutions Ltd as the SHEQ Compliance Lead in November 2023.
HSE Qualifications:
- NEBOSH International Diploma for Occupational Health and Safety
- NEBOSH National General Certificate in Occupational Health and Safety
- NEBOSH Environmental Management Certificate
- NEBOSH Fire Safety and Risk Management Certificate
- IOSH Managing Safely
- NATAS Asbestos Awareness
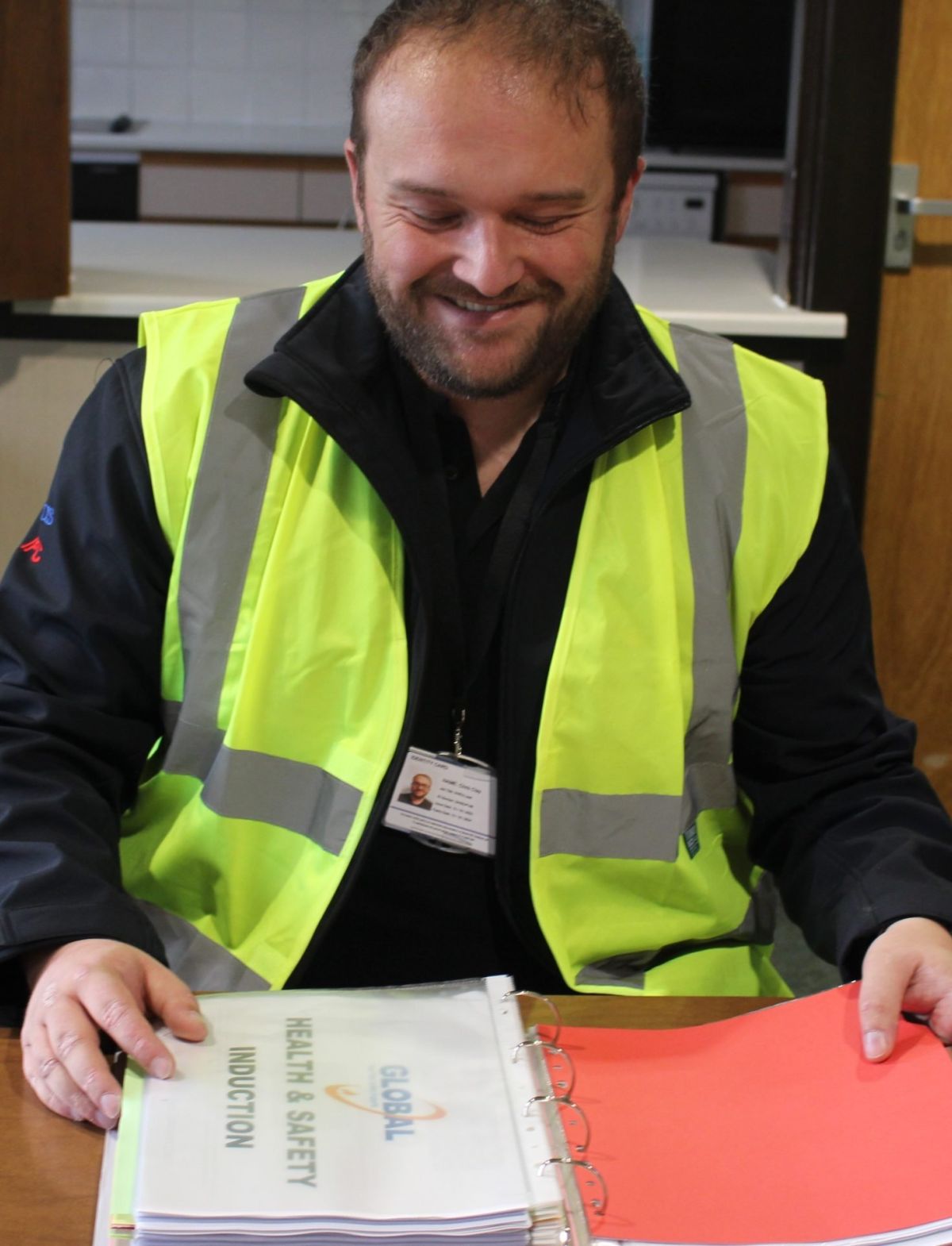
FAQs
In the UK, businesses may require the expertise of a health and safety consultant for various reasons. These professionals specialize in advising organizations on compliance with health and safety regulations to establish a secure working environment. Here are situations when you might need a consultant:
-
New Business Setup: Ensure a robust health and safety system from the start.
-
Risk Assessments: Identify and manage potential risks through regular assessments.
-
Compliance with Legislation: Stay updated with changing regulations to ensure legal compliance.
-
Incident Investigation: Conduct thorough investigations after workplace incidents and recommend preventive measures.
-
Specialized Expertise: Address industry-specific challenges with a consultant experienced in your sector.
-
Employee Training: Provide training programs to raise awareness of hazards and promote safe practices.
-
Contractor Management: Ensure contractors adhere to regulations and integrate into your safety management system.
-
Workplace Inspections and Audits: Conduct regular assessments, identify hazards, and recommend improvements.
-
Crisis Management: Handle health and safety crises effectively, implementing emergency measures.
-
Continuous Improvement: Establish a culture of ongoing improvement in health and safety practices.
The need for a health and safety consultant varies based on business size, nature, and industry. Consulting with professionals ensures legal obligations are met, creating a safe working environment.
The frequency of inspections by the UK Health and Safety Executive (HSE) can vary based on several factors, including the industry, the level of risk associated with the activities, and the organization’s compliance history. The HSE prioritizes inspections based on risk assessment and aims to focus its resources on sectors and businesses where the potential for harm is highest.
In general, the HSE employs a proactive and targeted approach to inspections, aiming to address areas of significant risk and potential non-compliance. Some factors influencing the frequency of inspections include:
High-Risk Industries:
Industries with inherently higher risks, such as construction, manufacturing, and chemical processing, may experience more frequent inspections.
Previous Incidents or Non-compliance:
If a workplace has a history of accidents, incidents, or non-compliance with health and safety regulations, it may be subject to more frequent inspections.
Complaints or Reports:
The HSE may conduct inspections in response to complaints from workers, members of the public, or other stakeholders. Reports of unsafe practices or conditions can trigger an investigation.
Targeted Campaigns:
The HSE may launch targeted inspection campaigns focusing on specific industries, hazards, or compliance issues. These campaigns are designed to address widespread concerns and improve overall safety standards.
Routine Inspections:
Some businesses may experience routine, scheduled inspections as part of the HSE’s ongoing efforts to monitor compliance across various sectors.
It’s important for businesses to be aware of their legal obligations, conduct regular risk assessments, and implement robust health and safety management systems. This proactive approach can help mitigate risks and reduce the likelihood of enforcement actions or unexpected inspections by the HSE.
Businesses should regularly check the HSE website and other official communications for updates on inspection priorities, guidance, and changes to health and safety regulations to stay informed about potential areas of focus for the HSE.
Risk Assessments:
Inspectors review the organization’s risk assessments to ensure the identification of potential hazards and the implementation of appropriate control measures.
Health and Safety Policies:
The existence and effectiveness of a comprehensive health and safety policy are examined to guide the organization’s safety practices.
Workplace Conditions:
The overall workplace condition, including cleanliness, organization, and identification of potential hazards or unsafe conditions, is assessed.
Training and Competence:
Inspectors evaluate whether employees have received sufficient health and safety training and possess the necessary competence for safe task execution.
Emergency Procedures:
Reviewing emergency procedures, inspectors assess employee awareness and training to follow them in case of an emergency.
Use of Personal Protective Equipment (PPE):
Adequate use of personal protective equipment is scrutinized to ensure employee protection from workplace hazards.
Machinery and Equipment Safety:
The proper maintenance, regular inspection, and inclusion of necessary safety features in machinery and equipment are checked.
Workplace Transport:
For applicable scenarios, inspectors assess the safety of workplace transport systems, including vehicles, forklifts, and other mobile equipment.
Chemical and Hazardous Substances Handling:
Inspection includes a review of storage, handling, and control measures for hazardous substances to prevent exposure and minimize risks.
Welfare Facilities:
The provision of adequate welfare facilities, such as rest areas, sanitation, and first aid, is examined to ensure employee well-being.
Compliance with Legislation:
Compliance with relevant health and safety legislation and regulations, including the Health and Safety at Work Act, is verified.
Record-Keeping:
Organizations are expected to maintain records related to health and safety, including risk assessments, training records, and incident reports, which inspectors may review during an inspection.
It’s crucial for organizations to proactively manage health and safety, conduct regular risk assessments, and promptly address identified issues to ensure regulatory compliance and foster a safer working environment for employees.
In the United Kingdom, the Health and Safety Executive (HSE) has the authority to conduct unannounced inspections at workplaces. Inspections can occur without prior notice, and inspectors may arrive at a business premises to assess compliance with health and safety regulations. This unannounced approach is part of the HSE’s strategy to ensure that they observe workplace conditions as they are on a day-to-day basis, without giving businesses the opportunity to prepare.
During an unannounced inspection, HSE inspectors will typically assess various aspects of health and safety, as mentioned in a previous response, including risk assessments, workplace conditions, training, equipment safety, and compliance with relevant legislation. The goal is to identify potential hazards, assess the effectiveness of control measures, and ensure that businesses are meeting their legal obligations to provide a safe working environment.
Businesses need to be proactive in managing health and safety, conducting regular risk assessments, and maintaining compliance with regulations to minimize the likelihood of enforcement actions resulting from unannounced inspections. Being prepared for inspections by having robust health and safety policies, procedures, and records in place can help organizations respond effectively when inspectors visit.
If an organization fails a Health and Safety Executive (HSE) inspection in the UK, it means that the inspectors have identified serious shortcomings or non-compliance with health and safety regulations. The consequences of failing an inspection can vary based on the severity of the issues found and the organization’s history of compliance. Here are some potential outcomes:
Enforcement Notices:
The HSE may issue enforcement notices specifying the improvements that need to be made to address the identified health and safety deficiencies. There are two main types of enforcement notices: Improvement Notices, which require specific actions to be taken within a specified timeframe, and Prohibition Notices, which prohibit certain activities until safety concerns are addressed.
Prosecution:
In cases of serious breaches or persistent non-compliance, the HSE may choose to take legal action through prosecution. This can result in criminal charges against the organization, leading to fines and potential imprisonment of individuals responsible for the breaches.
Fines:
Fines may be imposed as a result of prosecution or as an alternative to prosecution. The amount of the fine can vary depending on the severity of the health and safety failings.
Publicity:
Details of enforcement action taken by the HSE, including prosecution outcomes and fines, may be publicized. This can impact the organization’s reputation and may have financial and operational consequences.
Impact on Business Operations:
In severe cases, enforcement action could result in the temporary or permanent closure of all or part of the business until safety concerns are adequately addressed.
Reputational Damage:
Failing an HSE inspection can lead to reputational damage, affecting relationships with clients, customers, suppliers, and other stakeholders.
It’s important to note that the consequences will depend on the specific circumstances of the inspection findings. Businesses are encouraged to take immediate action to address any identified health and safety deficiencies, cooperate with the HSE, and implement corrective measures outlined in enforcement notices. Proactive engagement in improving health and safety standards can help mitigate the impact of enforcement actions and contribute to the overall well-being of employees and the organization. Regular self-assessment and compliance with health and safety regulations are key components of maintaining a safe working environment.